0 引言
近年来,定向井在世界各地油气田开发中得到了迅速发展。定向井的井眼轨迹在空间是三维弯曲的,抽油杆在油管内运动时不可避免地发生摩擦[1],导致抽油杆与油管之间发生偏磨,甚至油管被磨穿孔。在抽油杆上加装扶正器是防治油井杆管偏磨的措施之一[2],但扶正器使抽油杆由静定问题变成了变刚度的静不定问题,给杆柱设计带来了更大的困难。
20世纪90年代,国内诸多学者提出了扶正器的安装和间距设计方法[3-5]。饶建华等[6]提出了定向井有杆抽油系统扶正器三维可视化设置及仿真技术;吴奇等[7]揭示出含聚黏弹流体杆柱弯曲的影响,找到了聚驱抽油机井杆柱扶正器合理布置新方法;王文昌等[8]考虑了抽油杆柱的超长细比及井眼的非线性约束特征,用搜索迭代法设计了抽油杆柱扶正器位置。事实上,定向井中抽油杆柱的变形、受力和运动是杆柱在狭长弯曲、充满井液的管道中的复杂力学问题。实践中,按设计间距在偏磨井段下入扶正器后,出现偏磨井段上移或下移的现象,这可能是将抽油杆接箍以及扶正器假定为等截面积直杆造成的[9-11]。笔者考虑带有扶正器的抽油杆柱在油管内往复过程中,受“风洞”[12]及“活塞”[13]效应的影响,按抽油杆柱受力状况和井眼尺寸分别确定扶正器的间距,然后取其最小值,从而延长抽油杆与油管的磨损时间。
1 扶正器间距上的正压力合力 1.1 定向井某井段的狗腿角将被测井段的井眼轨迹简化为一条圆弧线,即一条平面曲线,用 Lubinski公式[14]确定被测井段的狗腿角β,即有:

式中:α为井斜角;φ为方位角,Δφ=|φ2-φ1|。
1.2 计算斜井井段正压合力或单位长度正压力抽油杆杆柱在上、下冲程时最下端受到的各种载荷是不同的[4],可用其正压合力或单位长度正压力来表征。
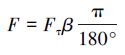

式中:F为斜井段抽油杆柱上的正压合力,N;f为斜井段抽油杆柱上的单位长度正压力,N/m;Fτ为斜井段抽油杆柱两端的轴向力,N;βL为斜井段狗腿度;ΔL为相邻测点间的距离,即斜井井段弧长或点距,m。
1.3 扶正器间距上的正压力合力和摩擦力合力扶正器间距上的正压力F1和摩擦力合力f1的计算式为:


式中:μ为扶正器与油管间的摩擦因数,无量纲;Δl′为扶正器间距的长度,m。
2 斜井段抽油杆柱的最大挠度根据弯曲变形理论[15-16],相邻2扶正器间抽油杆柱的最大挠度为:

式中:E为材料弹性模量,对于钢材,E=210 GPa;I为截面惯性矩,对于圆截面 ,I=πd4/64,cm4;fmax为相邻2扶正器之间抽油杆柱的最大挠度,cm。
3 扶正器的间距确定 3.1 按受力抽油杆柱受力状况确定扶正器的间距带有扶正器的抽油杆柱在油管内是一细长杆,将相邻2扶正器之间的抽油杆柱简化成简支梁结构,按压杆处理[17]。依据抽油杆、抽油杆接箍和扶正器不与油管内壁相接触的原则,扶正器间距的长度为:
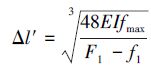

式中:Df为扶正器外径,cm;df为抽油杆本体或其接箍外径,cm。
3.2 按井眼尺寸确定定扶正器的间距带有扶正器的抽油杆柱在油管内也可以看成是平面或空间上的连续直梁[18],扶正器作为轴心,按绕轴心转动的抽油杆柱的弯曲正应力是交变的原则,扶正器间距的长度为:


式中:δ为扶正器外径许可的单边磨损量,一般取2~4 mm;R为井眼中心线曲率半径,m。
3.3 确定扶正器合理间距Δlf
对式(1) ~式(11) ,应用直接搜索迭代法进行迭代计算[19-20],最终得到扶正器合理的安放位置。
4 现场应用2010年至今,定向井防偏磨用扶正器下入位置的确定方法在1 000余口偏磨的定向油井应用。应用结果表明:油井检泵周期平均延长518 d并正在延续;造斜点最高 421 m,最大井斜49.03°,平均造斜点高度1 039 m,平均最大井斜深度1 792 m,平均最大井斜23.4°。
典型井例:X5-34 井,造斜点最高417 m,最小井斜角6.21°,最大井斜角45.19°,斜井井段1 968 m,在645、813和1 075 m处进行3次增斜;油井曾2次因抽油杆接箍偏磨断裂而检泵,检泵周期226 d;2013-11-04检泵,泵深1 850 m,下入122个扶正器,油井正常生产至今,现已连续生产828 d。
5 结论(1) 在定向井抽油杆柱上加装扶正器,可以有效地防止油井抽油杆与油管之间的偏磨。
(2) 带有扶正器的抽油杆柱在油管内因扶正器外径增大,受到“风洞”及“活塞”效应的影响,按抽油杆柱受力状况和井眼尺寸分别确定扶正器的间距,应用直接搜索迭代法求解,然后取其最小值,这样更接近现场实际。
(3) 扶正器下入井段在油井每次检泵作业时,根据现场抽油杆和油管的实际磨损情况进行修正。
[1] | 付亚荣. 定向井防偏磨内衬油管下入井段的确定[J]. 新疆石油天然气, 2015, 11 (1) : 65–67 . |
[2] | 黄忠桥, 罗雄, 魏红燕, 等. 三维井眼抽油杆扶正器间距配置计算方法[J]. 石油钻采工艺, 2010, 32 (3) : 60–64 . |
[3] | 李淑芳, 甘子泉. 直井抽油杆柱扶正器安装位置及安装间距[J]. 石油机械, 1999, 27 (1) : 52–55 . |
[4] | 覃成锦, 胡小兵, 高德利. 斜井抽油杆扶正器安放间距三维计算[J]. 石油机械, 1997, 25 (5) : 45–48 . |
[5] | 佘梅卿, 申秀丽. 稠油斜直井抽油杆扶正器安放间距计算[J]. 石油机械, 1997, 25 (12) : 7–9 . |
[6] | 饶建华, 刘宏昭, 董江峰, 等. 定向井有杆抽油系统扶正器可视化设置及仿真[J]. 海洋石油, 2006, 26 (2) : 75–78 . |
[7] | 吴奇, 刘合, 师国臣. 聚驱抽油机井杆柱扶正器合理布置新方法[J]. 石油钻采工艺, 2004, 26 (3) : 52–54 . |
[8] | 王文昌, 白楠, 狄勤丰, 等. 定向井抽油杆柱扶正器位置设计新方法[J]. 钻采工艺, 2015, 38 (6) : 49–52 . |
[9] | 王治国, 徐璧华, 陈超, 等. 复杂井眼条件下扶正器对套管下入摩阻的影响研究[J]. 钻采工艺, 2014, 37 (1) : 27–30 . |
[10] | 章敬, 高飞, 江洪, 等. 稠油定向井扶正器优选及分布设计[J]. 钻采工艺, 2014, 37 (2) : 48–50 . |
[11] | 孙聪聪, 檀朝东, 赵明, 等. 考虑接箍和扶正器的三维抽油杆柱优化设计[J]. 中国石油和化工, 2014 (4) : 56–59 . |
[12] | 李子丰, 蔡雨田, 李冬梅, 等. 地层测试管柱力学分析[J]. 石油学报, 2011, 32 (4) : 709–716 . |
[13] | 曾志军, 胡卫东, 刘竟成, 等. 高温高压深井天然气测试管柱力学分析[J]. 天然气工业, 2010, 30 (2) : 85–87 . |
[14] | 高志强. 关于全角变化率的探讨[J]. 石油钻采工艺, 1985, 7 (3) : 35–38 . |
[15] | 李远超, 吴晓东, 吕彦平, 等. 螺杆泵采油井扶正器位置设计动力学研究[J]. 石油钻采工艺, 2007, 27 (5) : 67–70 . |
[16] | 李国锋, 徐鑫, 赵勇, 等. 水平井固井液压式套管扶正器的改进与应用[J]. 石油钻采工艺, 2015, 37 (4) : 54–57 . |
[17] | 佘梅卿. 空心抽油杆采油系统扶正器安放间距计算[J]. 石油矿场机械, 2005, 34 (5) : 51–54 . |
[18] | 隋允康, 任旭春. 斜井单螺杆抽油泵柱和扶正器间距的最优设计[J]. 计算力学学报, 2002, 19 (1) : 59–62 . |
[19] | 姚侗, 何淦瞳. 线性规划的一种新算法——直接搜索迭代法[J]. 高校应用数学学报A辑, 1997, 12 (1) : 73–84 . |
[20] | 高德利, 郑传奎, 覃成锦. 蠕变地层中含缺陷套管外挤压力分布的数值模拟[J]. 中国石油大学学报(自然科学版), 2007, 31 (1) : 56–62 . |