0 引言
随着油气勘探进程的不断拓展和勘探区域的不断扩大,钻井过程中遇到研磨性强、可钻性差的难钻地层和复杂地层越来越多[1-2]。使用螺杆动力钻具的复合钻井技术经过快速发展和推广普及,在软—中硬地层中取得了显著的提速效果[3-4];但是随着井深的增加,岩石抗压强度增大、可钻性变差,使得现有井下动力钻具产生的高转速、大扭矩的旋转切削破岩方式,已经不足以有效克服岩石抗压强度吃入地层破碎岩石,从而造成破岩效率降低、钻头消耗量大等问题不断出现[5-7]。
旋冲钻井技术利用了硬地层岩石脆性大、抗剪强度低、不耐冲击等特点,通过在钻头上端加接一个轴向冲击工具,可以在钻头旋转破岩的同时对岩石施加一定频率的上下冲击力,从而起到提高破岩能量、加速岩石损伤破碎的效果[8-17]。
笔者在现有螺杆动力钻具结构特点基础上,引入旋冲钻井破岩理念及轴向机械冲击破岩功能,自主研制集成一体化的ZYXC-244机械式旋冲螺杆钻具,旨在实现大扭矩与轴向冲击协同作用的破岩效果,为难钻地层的提速提效提供有效的技术手段。
1 整体设计及结构 1.1 结构组成ZYXC-244机械式旋冲螺杆采用一体化设计,分别由旁通阀总成、动力总成、传动总成和冲击总成4部分集合而成(图 1)。其中旁通阀总成、动力总成和传动总成与常规螺杆结构组成相近,而冲击总成接在传动总成下方,并且进行创新设计,内部包含有实现机械启振冲击功能的凸轮机构,冲击总成主要零件由上传动轴、中接头、滚轮座、滚轮、凸轮、外壳体、下传动轴、壳体接头、防掉环和下接头等组成。
![]() |
图 1 ZYXC-244机械式旋冲螺杆整体结构设计图 Fig. 1 Structural diagram of the ZYXC-244 mechanical rotary-percussive tool based on screw drill |
|
由ZYXC-244机械式旋冲螺杆的整体结构设计图(图 1)可知,其工作原理为:钻井液通过旁通阀总成进入钻具内部,驱动动力总成中的马达转子产生高转速和大扭矩的输出能量,并通过传动总成带动上传动轴旋转。由于上传动轴既是传动总成的传动部件又是冲击总成的冲击部件,其在冲击总成内部首先通过六方传动面与凸轮相连,然后凸轮通过花键与下传动轴相连,而下传动轴通过螺纹又与下接头相连,因此凸轮、下传动轴和下接头也会随着上传动轴一起旋转,并将转速和扭矩传递给钻头。
根据图 2所示的凸轮与滚轮配合的结构特征可知,凸轮在旋转过程中推动滚轮沿着其螺旋提升面滚动,从而使得滚轮在滚动过程中带动工具上部结构(包括旁通阀总成、动力总成、传动总成和上传动轴等)提升,在螺旋面高点处的钻压作用下加速下落;并且在上传动轴与下传动轴之间产生一定频率和幅值的机械冲击载荷并通过下接头传递给钻头,可实现钻头在旋转+冲击联合作用下的协同破岩,改变传统单一切削破岩方式,提高破岩能量。
![]() |
图 2 ZYXC-244机械式旋冲螺杆凸轮机构示意图 Fig. 2 Schematic diagram of the cam mechanism of ZYXC-244 mechanical rotary-percussive tool based on screw drill |
|
ZYXC-244机械式旋冲螺杆的功能特点主要有:1)在输出常规回转切削能量的同时,还产生机械冲击能量,有效提高破岩能量;2)冲击过程中工具壳体可以产生轴向振动,有效降低工具与井壁摩阻,提高钻压传递效率;3)具备有可靠的防掉功能,充分满足安全钻井要求;4)可以根据现场工况配套相应弯角壳体,满足定向钻进要求;5)对钻井液密度和固相含量无特殊要求,且对MWD(measurement while drilling,随钻测量)及其他测量工具无影响。
2 性能参数分析机械式旋冲螺杆的冲击力、冲击频率和输出扭矩等性能参数是其实现提速提效的重要保证,通过建立冲击功、冲击频率和输出扭矩的计算模型,可明确性能参数的主要影响因素和变化规律,并进一步优选钻压和排量等钻井参数。
1) 冲击功
建立旋冲螺杆在直径段工作时的钻柱力学模型(图 3)[18],模型将整个钻柱简化为钻杆和钻铤2部分,钻柱上端采用固定约束,钻柱在井眼内根据钻压波动而产生轴向弹性压缩和伸长,则有:
![]() |
K1.钻杆等效弹性系数;K2.钻铤等效弹性系数;K.整个钻柱等效弹性系数;H.提升高度的最大值;A.钻柱底部初始位置;B.钻柱底部提升H后的位置。 图 3 直井段钻柱力学模型 Fig. 3 Schematic diagram of the drill string mechanical model in vertical well |
|

式中:Ei(i=1, 2)为钻杆或钻铤弹性模量,MPa;Ai(i=1,2)是钻杆或钻铤截面积,m2;Li(i=1,2)是钻杆或钻铤长度,m。
图 3中,A位置为钻柱底部的初始位置,此时整个钻柱的钻压P=P0;开始工作后,工具冲击总成中的滚轮沿着凸轮螺旋面向上滚动并带动整个钻柱提升,机械能转化为钻柱的势能;当提升高度h达到最大值H后到达B位置,然后积攒的钻柱势能突然释放,并将势能转化为钻头破碎地层的冲击功,因此根据模型,旋冲螺杆冲击功W为
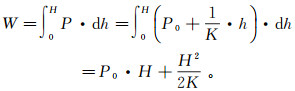
从式(2)可知,旋冲螺杆的冲击功主要与钻压和提升高度有关,图 4所示即为ZYXC-244机械式旋冲螺杆冲击功随钻压和提升高度的变化曲线,从图 4可知,冲击功大小随着钻压和提升高度的增大而增大。
![]() |
图 4 ZYXC-244机械式旋冲螺杆冲击功随钻压和提升高度的变化曲线 Fig. 4 Effect of impact energy on weight on bit and lifting height of ZYXC-244 mechanical rotary-percussive tool based on screw drill |
|
2) 冲击频率
当凸轮螺旋面个数为n时,凸轮每转动一周就实现整个钻柱上下运动n次,因此,工具的冲击频率Ff计算公式为

式中,r为马达转速,r/min。
根据马达转速与排量的关系,有

式中: Q为排量,L/s;q为马达每转一圈排量,L/r,一般而言,244 mm螺杆马达转子每转排量为32.25 L/r。
将式(4)代入式(3)中,得出冲击频率与排量和凸轮螺旋面个数的关系为

图 5为ZYXC-244机械式旋冲螺杆冲击频率随排量和凸轮螺旋面个数的变化曲线,从图 5可知, 冲击频率大小随着排量和凸轮螺旋面个数的增加而呈线性增大趋势。因此,通过优选螺旋面数量多的凸轮机构,可以在相同排量下获得更高的冲击频率。
![]() |
图 5 ZYXC-244机械式旋冲螺杆冲击频率随排量和凸轮螺旋面个数的变化曲线 Fig. 5 Effect of impact frequency on flow and number of helical surfaces on cam of ZYXC-244 mechanical rotary-percussive tool based on screw drill |
|
与此同时,在实际钻井过程中,为了充分利用工具的冲击频率和输出转速来最大限度地实现提速提效,应尽可能在钻井泵性能允许条件下采用大排量进行钻进。
3) 输出扭矩
由于工具冲击总成中的滚轮沿着凸轮螺旋面向上滚动并带动整个钻柱产生一个最大提升高度H的过程会对动力总成的输出扭矩产生损耗,因此,确定损耗扭矩T′与钻压P0和最大提升高度H的关系,有助于获取机械式旋冲螺杆的输出扭矩T。
![]() |
F′.滚轮在与凸轮相对运动过程中受到的水平方向反作用力,N;N.滚轮受到的沿垂直凸轮螺旋面方向的支撑力,N;f.滚轮受到的沿凸轮螺旋面方向的摩擦力,N;θ.凸轮螺旋面的提升角,rad。 图 6 凸轮机构受力分析 Fig. 6 Force analysis of the cam mechanism |
|

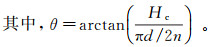
式中:μ为滚轮与凸轮之间的滚动摩擦系数;d为凸轮的等效中径,m;Hc为凸轮螺旋面高度,m。
因此,凸轮机构的损耗扭矩T′和工具的输出扭矩T为:


式中,T0为马达转子输出扭矩,kN·m。
由式(9)可知:在马达转子输出功率T0不变以及凸轮机构中的动摩擦系数μ、螺旋面高度Hc、螺旋面个数n和等效中径d确定之后,旋冲螺杆的输出扭矩T主要与初始钻压P0和最大提升高度H有关。
图 7为ZYXC-244机械式旋冲螺杆输出扭矩随钻压和提升高度的变化曲线,从图 7可知,旋冲螺杆的输出扭矩随着钻压和提升高度的增大而减小,并且提升高度越大,输出扭矩的下降幅度越明显。因此,通过优选提升高度较小的凸轮机构,可以有效降低输出扭矩的损耗,提高旋冲螺杆的能量利用率。
![]() |
图 7 ZYXC-244机械式旋冲螺杆输出扭矩随钻压和提升高度的变化曲线 Fig. 7 Effect of output torque on weight on bit and lifting height of ZYXC-244 mechanical rotary-percussive tool based on screw drill |
|
结合图 4和图 7可知,旋冲螺杆使用过程中,钻压参数的选取主要根据地层岩性、井眼尺寸、钻头类型及抗冲击性能、提升高度等因素综合考虑。一般而言,Φ311.2 mm以上的PDC(金刚石复合片)钻头允许的冲击功为400~500 J,而相同尺寸的复合钻头允许的冲击功为500~600 J。当在砂岩、粉砂质泥岩地层使用旋冲螺杆配合PDC钻头进行钻进时,优选提升高度为3 mm的凸轮机构,并得出工具最优的钻压参数为12~16 t;当使用旋冲螺杆配合复合钻头钻进时,优选提升高度为5 mm的凸轮机构,并得出工具最优的钻压参数为10~12 t。
3 防掉功能原理设计防掉功能是保证工具井下安全的关键,其作为工具可靠性的最后一道防线,直接关系到工具的使用安全和井下安全。因此,笔者在对ZYXC-244机械式旋冲螺杆进行结构和功能设计时,重点研发了针对冲击总成的防掉功能及相应的结构,以使工具在冲击总成主要零件发生断裂或者脱扣时,均可实现防掉功能。
图 8所示是ZYXC-244机械式旋冲螺杆防掉功能效果示意图,其中:
![]() |
a. 上传动轴上部断裂状态;b. 上传动轴中部断裂状态;c. 下传动轴上部断裂状态;d. 下传动轴下部断裂状态;e. 外壳体断裂或者螺纹脱扣状态。 图 8 ZYXC-244机械式旋冲螺杆防掉功能效果示意图 Fig. 8 Effect diagram of the fall prevention function of ZYXC-244 mechanical rotary-percussive tool based on screw drill |
|
1) 当上传动轴上部出现断裂(图 8a)或者中部出现断裂(图 8b)时,断裂面以下的上传动轴带动凸轮、下传动轴、防掉环和下接头一起在重力作用下向外伸出,此时依靠下传动轴外部的变径台阶挂靠在壳体接头顶端实现防掉功能。
2) 当下传动轴上部出现断裂(图 8c)或者下部出现断裂(图 8d)时,断裂面以下的下传动轴带动下接头一起在重力作用下向外伸出,直至下传动轴下端面接触到与上传动轴下部环形卡槽配合连接的防掉环,从而实现防掉功能。
3) 当外壳体出现断裂或者连接螺纹出现脱扣(图 8e)时,冲击总成内部的凸轮、下传动轴和下接头一起在重力作用下向下伸出,直至下传动轴下端面接触到与上传动轴下部环形卡槽配合连接的防掉环;而此时断裂面或者松扣部位以下的外壳体带动壳体接头一起也在重力作用下向下伸出,并挂靠在下接头上端面,从而实现防掉功能。
4 现场应用ZYXC-244机械式旋冲螺杆先后在四川盆地大足气田和普光气田的足203H1-3井和大湾4011-2井进行了现场应用,具体应用情况如下:
4.1 足203H1-3井现场应用情况足203H1-3井位于四川盆地渝西区块蒲吕场向斜构造,ZYXC-244机械式旋冲螺杆在足203H1-3井三开Φ311.2 mm井眼进行了应用,井段是1 382~2 067 m,钻遇地层包括须家河组、雷口坡组、嘉陵江组五段至三段,岩性分别为石英砂岩、泥质砂岩、白云岩和灰岩。
通过表 1所示的足203H1-3井与邻井在同井段使用的工具类型、钻头类型、钻井参数对比情况可知,ZYXC-244机械式旋冲螺杆配合PDC钻头时采用的最优值与常规螺杆配合PDC钻头时相比,钻压减小了2~4 t,而与常规螺杆配合复合钻头时相比,钻压减小了4~6 t。
井号 | 动力工具类型 | 钻头类型 | 钻井参数 | ||
钻压/t | 转速/(r/min) | 排量/(L/s) | |||
足203H1-3 | ZYXC-244机械式旋冲螺杆 | PDC钻头 | 12~16 | 95~100 | 55~57 |
足203 | 7LZ244常规螺杆 | PDC钻头 | 16~18 | 95~100 | 50~60 |
足202-H1 | 7LZ244常规螺杆+5LZ216常规螺杆 | PDC钻头 | 14~18 | 95~100 | 50~56 |
足202 | 7LZ244常规螺杆+5LZ244常规螺杆 | 复合钻头 | 18~22 | 55~70 | 55~60 |
足201 | 7LZ216常规螺杆+5LZ216常规螺杆 | PDC钻头 | 14~18 | 95~100 | 55~60 |
ZYXC-244机械式旋冲螺杆在足203H1-3井进尺685.00 m,工具井下工作时间166 h,纯钻时间98.55 h,平均机械钻速6.95 m/h。
图 9为足203H1-3井与邻井同井段的起下钻次数和机械钻速对比,由图 9可知:
![]() |
图 9 足203H1-3井与邻井同井段起下钻次数与机械钻速对比 Fig. 9 Contrast on tripping times and ROP of Well Z203H1-3 and adjacent wells |
|
1) 足203H1-3井在使用ZYXC-244机械式旋冲螺杆井段与邻井同井段使用常规螺杆相比,机械钻速分别提高了38.2%、75.1%、166.3%和135.6%,表明与常规螺杆相比,旋冲螺杆使用的钻压参数更小,取得的机械钻速更高。
2) 足203H1-3井在使用ZYXC-244机械式旋冲螺杆井段,起下钻2次,与邻井同井段相比,分别节省起下钻2次、5次、3次和3次,即分别节省钻头2只、5只、3只和3只,表明旋冲螺杆产生的轴向冲击作用不但不会对钻头产生损害,反而有助于改善钻头工况、延长钻头使用时间。
4.2 大湾4011-2井现场应用情况大湾4011-2井位于四川盆地川东断褶带大湾—雷音铺背斜带大湾构造,ZYXC-244机械式旋冲螺杆在大湾4011-2井二开Φ320 mm井眼进行了应用,井段为1 667.35~1 739.86 m,钻遇地层为须家河组,岩性为中砂岩、粗砂岩、粉砂质泥岩。
通过表 2所示的大湾4011-2井与邻井在同井段使用的工具类型、钻头类型、钻井参数对比情况可知,ZYXC-244机械式旋冲螺杆配合复合钻头时采用的最优值与常规螺杆配合复合钻头时相比,其钻压减小了4~5 t。
井号 | 井段/m | 动力工具类型 | 钻头类型 | 钻井参数 | ||
钻压/t | 转速/(r/min) | 排量/(L/s) | ||||
大湾4011-2 | 1 590.00~1 667.35 | 7LZ244常规螺杆 | 复合钻头 | 12~16 | 62~68 | 58~60 |
1 667.35~1 739.86 | ZYXC-244机械式旋冲螺杆 | 8~12 | 60~65 | 55~60 | ||
大湾4011-3 | 1 590.00~1 740.00 | 7LZ244常规螺杆 | 复合钻头 | 12~17 | 60~65 | 55~60 |
ZYXC-244机械式旋冲螺杆在大湾4011-2井进尺72.53 m,纯钻时间15.12 h,机械钻速4.80 m/h,与该井上趟钻在须家河组地层使用常规螺杆配合复合钻头的机械钻速2.76 m/h相比,提高了73.9 %,与邻井大湾4011-3井同井段使用常规螺杆配合复合钻头的机械钻速3.65 m/h相比,提高了31.5%。
5 结论1) 在现有螺杆动力钻具结构特点的基础上,引入了旋冲钻井破岩理念及轴向机械冲击破岩功能,成功研制了集合旁通阀总成、动力总成、传动总成和冲击总成于一体的ZYXC-244机械式旋冲螺杆。
2) 通过对ZYXC-244机械式旋冲螺杆主要性能参数的分析研究,建立了冲击功、冲击频率和输出扭矩的计算模型,获取了工具的性能参数变化曲线,并优选了适用于不同类型钻头的最优钻压参数。
3) 通过对ZYXC-244机械式旋冲螺杆防掉功能的创新设计,使得工具在冲击总成主要零件发生断裂或者脱扣时,均可以实现防掉功能,提高了工具可靠性,确保了井下安全。
4) ZYXC-244机械式旋冲螺杆先后在足203H1-3井和大湾4011-2井进行了现场应用,与常规螺杆相比,使用旋冲螺杆的钻压参数更小,取得的机械钻速更高,并且轴向冲击作用不但不会对钻头产生损害,反而有助于改善钻头工况、延长钻头使用时间。
[1] |
张瀚之, 翟晓鹏, 楼一珊. 中国陆相页岩油钻井技术发展现状与前景展望[J]. 石油钻采工艺, 2019, 41(3): 265-271. Zhang Hanzhi, Zhai Xiaopeng, Lou Yishan. Development Status and Prospect of the Drilling Technologies Used for Continental Shale Oil Reservoirsin China[J]. Oil Drilling & Production Technology, 2019, 41(3): 265-271. |
[2] |
汪海阁, 葛云华, 石林. 深井超深井钻完井技术现状、挑战和"十三五"发展方向[J]. 天然气工业, 2017, 37(4): 1-8. Wang Haige, Ge Yunhua, Shi Lin. Technologies in Deep and Ultra-Deep Well Drilling: Present Status, Challenges and Future Trend in the "13th Five-Year" Plan Period (2016-2020)[J]. Natural Gas Industry, 2017, 37(4): 1-8. |
[3] |
邱自学, 王璐璐, 徐永和, 等. 页岩气钻井螺杆钻具的研究现状及发展趋势[J]. 钻采工艺, 2019, 42(2): 36-37. Qiu Zixue, Wang Lulu, Xu Yonghe, et al. Status Quo and Development Trend of Positive Displacement Motor Used in Shale Gas Drilling[J]. Drilling & Production Technology, 2019, 42(2): 36-37. |
[4] |
苏义脑. 螺杆钻具研究及应用[M]. 北京: 石油工业出版社, 2001: 69-76. Su Yinao. Research and Application of Screw Drill[M]. Beijing: Petroleum Industry Press, 2001: 69-76. |
[5] |
黄仁山. 油气工业可借鉴的冲击回转钻进技术[J]. 石油钻探技术, 1996, 24(4): 18-20. Huang Renshan. The Percussion Rotary Drilling Technique that Can Be Learned by Oil and Gas Industry[J]. Petroleum Drilling Techniques, 1996, 24(4): 18-20. |
[6] |
殷琨, 王茂森, 彭枧明, 等. 冲击回转钻进[M]. 北京: 地质出版社, 2010: 52-57. Yin Kun, Wang Maosen, Peng Jianming, et al. Percussion Rotary Drilling[M]. Beijing: Geology Publishing House, 2010: 52-57. |
[7] |
陶兴华. 提高深井钻井速度的有效技术方法[J]. 石油钻采工艺, 2001, 23(5): 4-8. Tao Xinghua. Effective Measures for Improving the Penetration Rate of Deep Well[J]. Oil Drilling & Production Technology, 2001, 23(5): 4-8. DOI:10.3969/j.issn.1000-7393.2001.05.002 |
[8] |
李国华, 鲍洪志, 陶兴华. 旋冲钻井参数对破岩效率的影响研究[J]. 石油钻探技术, 2004, 32(2): 4-7. Li Guohua, Bao Hongzhi, Tao Xinghua. Effects of Drilling Conditions on Crushing Rocks While Rotary Percussion Drilling[J]. Petroleum Drilling Techniques, 2004, 32(2): 4-7. DOI:10.3969/j.issn.1001-0890.2004.02.002 |
[9] |
王雷, 郭志勤, 张景柱, 等. 旋冲钻井技术在石油钻井中的应用[J]. 钻采工艺, 2005, 28(1): 8-10. Wang Lei, Guo Zhiqin, Zhang Jingzhu, et al. Application of Percussive-Rotary Drilling Technology in Oil Wells[J]. Drilling & Production Technology, 2005, 28(1): 8-10. DOI:10.3969/j.issn.1006-768X.2005.01.003 |
[10] |
蒋宏伟, 刘永胜, 翟应虎, 等. 旋冲钻井破岩力学模型的研究[J]. 石油钻探技术, 2006, 34(1): 13-16. Jiang Hongwei, Liu Yongsheng, Zhai Yinghu, et al. Research on Rock-Crushing Mechanics Model in Rotary and Percussive Drilling[J]. Petroleum Drilling Techniques, 2006, 34(1): 13-16. DOI:10.3969/j.issn.1001-0890.2006.01.004 |
[11] |
Saksala T, Fourmeau M, Kane P A, et al. 3D Finite Elements Modelling of Percussive Rock Drilling: Estimation of Rate of Penetration Based on Multiple Impact Simulations with a Commercial Drill Bit[J]. Computers & Geotechnics, 2018, 99: 55-63. |
[12] |
Kong X, Fang Q, Wu H, et al. Numerical Predictions of Cratering and Scabbing in Concrete Slabs Subjected to Projectile Impact Using a Modified Version of HJC Material Model[J]. International Journal of Impact Engineering, 2016, 95: 61-71. DOI:10.1016/j.ijimpeng.2016.04.014 |
[13] |
Bu Changgen, Qu Yegao, Cheng Zhiqiang, et al. Numerical Simulation of Impact on Pneumatic DTH Hammer Percussive Drilling[J]. Journal of Earth Science, 2009, 20(5): 225-232. DOI:10.1007/s12583-009-0073-5 |
[14] |
Yin Qilei, Peng Jianming, Bo Kun, et al. Study on Dust Control Performance of a Hammer Drill Bit[J]. International Journal of Mining, Reclamation and Environment, 2013, 27(6): 393-406. DOI:10.1080/17480930.2013.787703 |
[15] |
景英华, 袁鑫伟, 姜磊, 等. 高速旋转冲击钻井破岩数值模拟及现场试验[J]. 中国石油大学学报(自然科学版), 2019, 43(1): 75-80. Jing Yinghua, Yuan Xinwei, Jiang Lei, et al. Numerical Simulation and Field Experimental Study on Rock Breaking in High Speed Rotating Percussion Drilling[J]. Journal of China University of Petroleum (Edition of Natural Science), 2019, 43(1): 75-80. DOI:10.3969/j.issn.1673-5005.2019.01.009 |
[16] |
张鑫鑫, 彭枧明, 孙铭泽, 等. 基于CFD的高能射流式液动冲击器活塞与缸体密封特性研究[J]. 吉林大学学报(地球科学版), 2017, 47(2): 534-541. Zhang Xinxin, Peng Jianming, Sun Mingze, et al. Study on the Sealing Characteristics Between the Piston and Cylinder in the High-Energy Liquid-Jet Hammer Based on CFD Method[J]. Journal of Jinlin University(Earth Science Edition), 2017, 47(2): 534-541. |
[17] |
李国琳, 葛东, 杨正龙, 等. 基于激光三角测量的射流式液动潜孔锤全行程实时运动规律试验[J]. 吉林大学学报(地球科学版), 2021, 51(1): 185-191. Li Guolin, Ge Dong, Yang Zhenglong, et al. Experiment of Real-Time Motion Law of Fluidic Hammer in Stroke Based on Laser Triangulation[J]. Journal of Jinlin University(Earth Science Edition), 2021, 51(1): 185-191. |
[18] |
韩志勇. 垂直井眼内钻柱的轴向力计算及强度校核[J]. 石油钻探技术, 1995, 23(增刊1): 8-13. Han Zhiyong. Study on Axial Force Calculating and Strength Testing for Drilling in Vertical Holes[J]. Petroleum Drilling Techniques, 1995, 23(Sup. 1): 8-13. |