Research progress in fatigue behavior of soda lime/aluminosilicate glass
硅酸盐玻璃具有良好的光学特性、高强度、高硬度以及能够在高温下稳定使用等优良的物理性能。硅酸盐玻璃家族中,钠钙硅酸盐玻璃和铝硅酸盐玻璃是最常用于飞机风挡、装甲防护等民用和国防军工领域的材料[1]。飞机风挡作为机体结构的一部分,由于服役环境比较苛刻,在实际使用过程中,不仅要经历高温(≈70 ℃)、低温(≈-55 ℃)以及高低温循环冲击,还有盐雾、霉菌等环境腐蚀[2]。因此要求其不仅具有耐划伤、耐冲击、高透过率、耐高低温冲击等性能,而且必须具有足够的结构强度、刚度和疲劳寿命[3]。据统计,在飞机构件的断裂失效中疲劳失效占80%以上[4],造成了重大的经济损失及人员伤亡。因此,研究玻璃的静态疲劳与动态疲劳行为对制备出具有高强度和长疲劳寿命的玻璃材料具有重大的意义。
玻璃的静态疲劳是指恒载过程下的延迟破坏,其主要来源是应力腐蚀条件下的亚临界裂纹扩展[5]。在恒载荷作用下,玻璃中逐渐出现微裂纹,随时间的延长,裂纹缓慢扩展。当其达到临界尺寸时,玻璃发生失稳破坏。在玻璃服役期间,裂纹的萌生与裂纹的扩展速率对玻璃的使用寿命有着重要的影响[6]。不同环境下的裂纹扩展速率截然不同,其中水蒸气作用下的亚临界裂纹扩展行为最为常见,其疲劳曲线通常分为3个阶段,该曲线可以预测玻璃的疲劳寿命。玻璃的动态疲劳是变化载荷下的延迟破坏[7]。在循环载荷的作用下玻璃中裂纹不断扩展,不同的循环应力下裂纹扩展速率不同,直至达到临界断裂应力玻璃发生断裂。
钠钙/铝硅酸盐玻璃的疲劳行为对其性能和寿命具有重要的影响,因此国内外研究人员开展了大量的研究[8-12]。本文对钠钙/铝硅酸盐玻璃疲劳的研究进展进行了综述:第一部分简述硅酸盐玻璃疲劳行为的原理及研究方法;第二和第三部分着重介绍钠钙硅酸盐玻璃和铝硅酸盐玻璃疲劳行为研究的国内外进展;第四部分总结了钠钙硅酸盐玻璃与铝硅酸盐玻璃疲劳行为的异同并对硅酸盐玻璃疲劳行为的研究方向进行了展望。
1 硅酸盐玻璃疲劳行为的原理及实验方法
1.1 疲劳失效过程及原理
疲劳失效是工件在应力和应变长期反复作用下发生损伤和断裂的现象[13-14]。对于硅酸盐玻璃,其静态疲劳寿命取决于应力腐蚀条件下的亚临界裂纹扩展速率,当应力强度因子随裂纹扩展速率变化达到断裂韧度KⅠC时,玻璃发生断裂。图 1为硅酸盐玻璃典型的V-KⅠ曲线[5],由该曲线可以确定其断裂韧度等力学性能。
在区域Ⅰ,裂纹扩展速率与玻璃的疲劳行为密切相关。裂纹扩展速率是关于应力强度因子KⅠ的增函数。裂纹扩展受裂纹尖端Si—O—Si键与水反应速率的限制,裂纹扩展速率随外加应力和湿度的增大而增大,与空气的湿度几乎呈线性关系,并且随着温度的升高而增大。区域Ⅰ的裂纹扩展速率vⅠ可以通过式(1)计算[5]:
|
(1) |
式中:v0是起始裂纹扩展速率;pH2O为水蒸气的分压;p0为总大气压;R为气体常数;Ea为没有外力作用时玻璃裂纹尖端水解反应的活化能;α, A, m, b为4个可调参数。
由于裂纹扩展速率对应力强度因子KⅠ的依赖性很强,且KⅠ的变化范围有限,区域Ⅰ的曲线也可以用幂律表达式拟合[15],如式(2)所示:
|
(2) |
式中:K0为起始应力强度因子;n为裂纹扩展指数。
但是式(1)更直接地反映了不同组分的玻璃与裂纹尖端环境之间的关系,因此在描述玻璃裂纹扩展曲线区域I时使用最为广泛。
区域Ⅱ通常以平台的方式出现,裂纹扩展速率受外加应力影响很小且几乎不随应力强度因子KⅠ变化。但裂纹扩展会受到湿度的影响,随着湿度的增加,平台的高度也会增加。由于水蒸气向裂纹尖端的扩展速率受到限制逐渐变慢,裂纹扩展速率的增加也相应变慢。区域Ⅱ裂纹扩展较为稳定,如式(3)所示:
|
(3) |
式中:vⅡ为区域Ⅱ裂纹扩展速率;DH2O为水分子在空气中的扩散系数;pH2O为水蒸气的分压。
区域Ⅲ裂纹扩展速率与湿度无关,但裂纹扩展速率随着应力强度因子KⅠ值的增加迅速增大。在无水环境或在真空中,裂纹扩展曲线只能观察到区域Ⅲ中的部分。当KⅠ=KⅠC时,裂纹迅速扩展最终发生疲劳断裂[16]。
1.2 硅酸盐玻璃疲劳行为实验方法
1.2.1 静态疲劳实验方法
Wiederhorn等[17]最先将双悬臂梁法应用于玻璃静态疲劳的研究,其系统研究过几种硅酸盐玻璃的亚临界裂纹扩展行为和应力腐蚀机制,获得的V-KⅠ数据与普适的玻璃疲劳曲线吻合得很好。后来Evans[18]发展完善了双扭法研究脆性材料中的亚临界裂纹扩展行为的技术。这种方法简单,不需要实时观测裂纹长度,只需记录最初和最终的裂纹长度,就可得到裂纹扩展速率,因此引起了广泛关注。但是他认为应力强度因子与裂纹长度无关,后来该观点被Ciccotti等修正[19],增加了与试样几何形状有关的修正系数,扩展了方程的适用范围。后来Janssen[20]针对双悬臂梁法的缺点发明了双劈裂钻孔压缩实验方法,Crichton等[21]采用该方法系统研究了磷酸盐激光玻璃的亚临界裂纹扩展行为。表 1对上述3种方法进行了详细的介绍。
表 1 静态疲劳实验方法[22-24]
Table 1
Test method of static fatigue[22-24]
Experimental method |
Loading diagram |
Sample preparing |
Advantage |
Disadvantage |
Double-cantilever cleavage[22] |
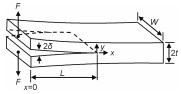 |
Cracks are made in the sample, and then load at the four points at the end of the sample |
Simple to operate and convenient to observe the process of crack growth |
Cracks grow too fast to get enough effective data points |
Double-cleavage-drilled compression[23] |
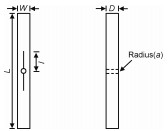 |
A hole is made in the center of the sample, and then loads at both two ends of the sample |
Improvement of the double-cantilever cleavage, and the crack growth rate will decrease during the test |
Hard to operate and control the load applied |
Double torsion[24] |
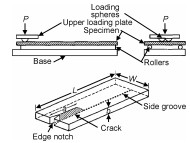 |
Cracks are made in the sample, and then four-point bending load is applied to the sample |
The crack grow at a constant rate, and the crack growth rate can be calculated only with the load |
The test error caused by making defects and equipment should be corrected |
1.2.2 动态疲劳实验方法
动态疲劳实验方法是对试样进行弯曲加载,最终得到断裂应力与加载速率的关系。所采用的玻璃试样包括含有维氏缺陷的玻璃试样和不含维氏缺陷的玻璃试样。最初研究玻璃的动态疲劳时,多采用不含维氏缺陷的玻璃试样进行四点弯曲加载,通过测得的断裂载荷得到加载速率与断裂应力的关系[7, 25]。但是在采用不含维氏缺陷的玻璃试样研究动态疲劳时,裂纹扩展长度与方向往往不能有效地控制,难以保证实验数据的真实性。
针对上述问题,Lawn等[14, 26-29]提出采用含有维氏缺陷的试样研究疲劳断裂的方法。该方法要求实验前采用维氏压头在玻璃表面预制压痕后进行四点弯曲加载,裂纹将沿着压痕径向扩展。与采用不含可控缺陷的试样分析方法相同,可以通过测量断裂载荷来确定加载速率与断裂强度的关系。采用含有可控缺陷的试样进行动态疲劳研究的主要优点是:第一,数据集中程度高,对实验结果处理更加精确;第二,裂纹沿压痕径向扩展,便于观察与收集数据。
2 钠钙硅酸盐玻璃的疲劳行为
2.1 钠钙硅酸盐玻璃的裂纹萌生
在玻璃表面微裂纹萌生及扩展理论中,Griffith微裂纹能量平衡扩展理论应用最为广泛[30]。Griffith理论把微裂纹尖端范围视作区域化线弹性体,该线弹性区域在能量平衡时处于稳定状态,一旦外力作用下使得该线弹性体变形能大于生成微裂纹产生的表面能时,就会形成微裂纹,并使微裂纹受力扩展。
压痕法是研究表面裂纹萌生的有效方法[31]。实验中可采用维氏压头、玻氏压头和立方角压头在玻璃表面制造压痕[32-34]。通过观察压头在不同载荷下产生径向裂纹的数量来确定裂纹萌生门槛值。Harding等[34]采用立方角压头研究了钠钙硅酸盐玻璃原片的裂纹萌生门槛值为0.5~1.5 mN。后来Koike等[35]研究化学强化钠钙硅酸盐玻璃在维氏压头下的径向裂纹萌生门槛值时发现,当化学强化钠钙硅酸盐玻璃表面压应力低于380 MPa时,其径向裂纹萌生门槛值低于原片玻璃,随着压应力的进一步增大,其径向裂纹萌生门槛值也随之增大。当表面压应力高于380 MPa时,化学强化钠钙硅酸盐玻璃的径向裂纹萌生门槛值高于原片玻璃。他们还通过对比原片玻璃与化学强化玻璃压痕残余应力场发现,造成这一现象的原因在于化学强化玻璃压痕周围产生的裂纹驱动力更大,因此更容易产生裂纹。随着压应力的增大,其对裂纹萌生的抑制作用更加明显[36]。当压应力足够大时,化学强化玻璃的裂纹萌生门槛值就会高于原片玻璃。
2.2 钠钙硅酸盐玻璃的亚临界裂纹扩展
主流观点认为应力腐蚀条件下的亚临界裂纹扩展是玻璃静态疲劳的主要来源[5],其中水对裂纹尖端的腐蚀作用是裂纹尖端应力腐蚀的重要组成部分。其主要机理有两个[37]:第一,因为水与玻璃中的Si—O—Si键发生化学反应导致键的断裂;第二,水中的氢离子与玻璃中的钠离子产生离子交换使玻璃裂纹尖端产生了一个张应力,从而可以加速裂纹的扩展[36]。
Wiederhorn[5]在研究钠钙硅酸盐玻璃的裂纹扩展规律时最先发现裂纹尖端的应力腐蚀主要是由于水与玻璃之间的化学反应,并且结合Charles和Hillig的静态疲劳理论[38],建立了在含有水蒸气的环境下计算裂纹扩展速率的表达式,如式(4)所示:
|
(4) |
式中:v是裂纹扩展速率;a,b是常数;x0是固定点水蒸气的摩尔分数;P是施加载荷。该式与普适的玻璃静态疲劳曲线的区域Ⅰ和区域Ⅱ吻合得很好,可以计算区域Ⅰ和区域Ⅱ的裂纹扩展速率。但是裂纹在区域Ⅲ的扩展与环境中水蒸气的量无关,因此不能采用该式来计算区域Ⅲ的裂纹扩展速率。目前区域Ⅲ的裂纹扩展曲线还未找到合适的表达式来描述。
在非水溶液中仍有少量水的存在,若水的含量与空气中水蒸气的含量相当,其静态疲劳曲线与玻璃在空气中的曲线大致相同。例如Freiman[39-40]在研究钠钙硅酸盐玻璃裂纹在庚烷中扩展时发现在相对湿度为50%庚烷中裂纹扩展曲线的位置和形状与在相对湿度为50%空气中的裂纹扩展曲线大致相同,在其他有机体中也有类似的结果。Wiederhorn的经典模型能够解释裂纹尖端没有钝化时的亚临界裂纹扩展行为,但是当在温度较高或水蒸气的压力较大时,裂纹尖端发生钝化,此时Wiederhorn的经典模型将不再适用。通常随着温度的升高,裂纹扩展速率更高,裂纹扩展阈值下降得更快[41]。Suratwala等[42]却得到了相反的结论,他们在研究氮气中水蒸气含量对裂纹扩展的影响时发现,Ⅰ区裂纹扩展速率随温度的升高而降低。这是由于随着温度升高,玻璃裂纹尖端游离的碱离子(例如钠钙硅酸盐中的钠离子)与水合氢离子发生离子交换,导致裂纹尖端附近产生压应力,从而抑制裂纹扩展[35]。同时离子交换能够导致裂纹尖端附近的表面发生膨胀,缩小两表面之间的距离,阻碍水继续向裂纹尖端渗透。压应力导致的裂纹尖端钝化是离子交换抑制裂纹扩展的一种形式,其通过改变裂纹附近玻璃的成分也能够达到抑制裂纹扩展的效果[43-44]。例如在Li+溶液中,Li+与钠钙硅酸盐玻璃裂纹尖端的Na+交换,从而使裂纹尖端附近的玻璃成分变为锂硅酸盐玻璃。锂硅酸盐玻璃的抗裂纹扩展性能强于钠钙硅酸盐玻璃,因此在裂纹尖端一定程度抑制了裂纹的扩展。
上述钠钙硅酸盐玻璃疲劳的研究主要是针对退火玻璃。而对于化学强化钠钙硅酸盐玻璃的静态疲劳研究有待进一步研究。
2.3 钠钙硅酸盐玻璃的动态疲劳
玻璃的动态疲劳研究始于20世纪中叶。1958年,Charles[7]首先提出了采用应力腐蚀模型来解释动态加载条件下的裂纹扩展,他提出动态疲劳是玻璃中出现的一种特殊的静态疲劳形式。在相同的变量下,瞬时应力水平和温度、压力以及大气成分控制着玻璃的破坏过程,任何成功地描述静态疲劳的分析模型都可以描述动态疲劳。因此Charles对静态疲劳理论进行修正并成功预测了加载速率对玻璃断裂强度的影响,从而奠定了玻璃动态疲劳研究的理论基础。描述断裂应力与应力加载速率关系如式(5)所示:
|
(5) |
式中:σf为断裂应力;β为常数;dσ/dt为应力加载速率。应力腐蚀指数主要根据动态疲劳曲线确定。后来Ritter[25]先后研究了酸蚀玻璃和磨损玻璃的动态疲劳行为,结果表明,对于各种硅酸盐玻璃,实验数据与Charles的方程拟合较好,特别是在高加载速率下,式(5)能够准确确定裂纹扩展指数n,从而验证了Charles的模型可以预测室温下断裂应力的准确性。Ritter在Charles的理论的基础上建立了动态疲劳的应力腐蚀模型,并针对可控缺陷试样的动态疲劳行为研究中的残余应力问题进行了修正。
此后,Lawn等[13, 26-28]将维氏压痕和划痕技术应用到脆性材料的动态疲劳研究中,实验前采用维氏压头在试样表面预制裂纹,使裂纹沿着压头径向扩展。但是在试样表面制造维氏压痕会产生残余应力[26, 45-46],主流观点认为降低残余应力会提高玻璃的力学性能[47],从而影响玻璃的疲劳行为。维氏压痕产生的残余应力会改变动态疲劳加载速率和断裂强度曲线的截距与斜率,若忽略残余应力的影响,最终得到的实验结果误差可高达两倍。为确定制造压痕时压头产生的残余应力对实验结果的影响情况,Marshall等通过对玻璃进行退火处理来进行对比分析,退火后玻璃实际的裂纹扩展指数n为13,小于忽略残余应力的预测范围16~19,从而证明了残余应力会加速玻璃的疲劳断裂,因此不能根据使用含有压痕缺陷试样实验得到的断裂数据直接预测玻璃的疲劳寿命。他们在后续的实验中引入了残余应力的影响,对之前的模型进行了修正,系统发展了含有可控缺陷的脆性材料动态疲劳模型。
后来Tomozawa等[48]试图验证Lawn等发现的压痕造成残余应力使动态疲劳裂纹扩展指数的增大的理论,但实验表明,完全释放残余应力所得到的n值变化量仅为动态疲劳过程中n值变化量的30%左右,因此残余应力释放理论不能解释玻璃的动态疲劳。为解释动态疲劳机理,他们采用细碳化硅粉研磨处理在玻璃表面制造缺陷,将处理后的玻璃在不同介质中进行动态疲劳实验,结果表明经过研磨处理后,玻璃的断裂强度随加载速率的增大而增大,裂纹尖端应力变化速率随裂纹的扩展而减小。研磨处理后的玻璃仅在水中表现出较强的加载速率依赖性,而在非水介质中,其加载速率依赖性非常小。水对玻璃的动态疲劳有着重要的作用[49],不同介质影响规律的差异归结于裂纹尖端的钝化和有限裂纹萌生应力的作用,这也是动态疲劳中n值变化的原因。他们还研究了假想温度对石英玻璃和钠钙玻璃动态疲劳行为的影响。研究发现随着玻璃假想温度的提高,其抵抗疲劳的能力逐渐增强。
随着对玻璃动态疲劳行为研究的深入,国内外科研工作者也开始关注浮法玻璃空气面和锡面的动态疲劳行为的差异以及玻璃疲劳损伤过程环境与裂纹的作用机理[50]。Sorarù等[51]研究了浮法钠钙硅酸盐玻璃在HF酸溶液中腐蚀后再在沸水中浸泡产生的表面改性对动态疲劳的影响,对含有维氏压痕的试样进行表面改性后,其动态疲劳行为变化不明显,而不含维氏压痕的试样表面改性后,其动态疲劳断裂强度有一定的变化。造成两者动态疲劳行为不同的原因是维氏压痕的深度与表面改性层深度的比值远大于1,导致表面改性的试样与未改性的试样无差异。Krohn等[52]研究了钠钙硅酸盐玻璃锡面与空气面动态疲劳行为的差异。结果表明,由于玻璃表面裂纹的深度大于锡的渗透深度,锡对玻璃应力腐蚀敏感性的影响无法体现,因此锡面与空气面动态加载下的裂纹扩展指数并无明显差异。同时他们提出,如果要精确测量锡对玻璃应力腐蚀敏感性的影响,需要观察与测量裂纹扩展的过程。
3 铝硅酸盐玻璃的疲劳行为
3.1 铝硅酸盐玻璃的裂纹萌生
与钠钙硅酸盐玻璃相比,铝硅酸盐玻璃具有更高的硬度与强度。Li等[53]等研究了化学强化铝硅酸盐玻璃的裂纹萌生门槛值的变化行为。图 2为铝硅酸盐玻璃裂纹萌生门槛值随化学强化时间的变化曲线,从图中可以看出铝硅酸盐玻璃原片锡面裂纹萌生门槛值为5.5~8.7 mN,远大于钠钙硅酸盐玻璃的裂纹萌生门槛值[34]。对于化学强化铝硅酸盐玻璃,其裂纹萌生门槛值随化学强化时间的延长而降低,这是由于随着强化时间的增加,化学强化铝硅酸盐玻璃表面压应力逐渐减小,这与钠钙硅酸盐玻璃相一致。但是原片铝硅酸盐玻璃的裂纹萌生门槛值高于化学强化铝硅酸盐玻璃,这恰恰与钠钙硅酸盐玻璃相反。因为采用立方角压头对化学强化铝硅酸盐玻璃制造压痕时产生的残余应力场大于原片玻璃,导致化学强化铝硅酸盐玻璃的裂纹驱动力显著高于原片铝硅酸盐玻璃,因此需要更高的表面压应力来阻止裂纹萌生,所以化学强化铝硅酸盐玻璃的裂纹萌生门槛值比原片玻璃低[6, 54-55]。他们还发现当压入载荷足够大时(9.5 mN),原片铝硅酸盐玻璃和化学强化铝硅酸盐玻璃表面均出现多条径向裂纹,并且原片玻璃径向裂纹长度明显大于化学强化玻璃。因此一旦裂纹出现,其扩展速率远大于化学强化玻璃,这是由于化学强化玻璃表面压应力能够显著抑制裂纹扩展[56-57]。表面压应力对裂纹萌生的抑制作用不明显,但对裂纹扩展过程表现出有效的阻碍作用。
对于浮法铝硅酸盐玻璃,其锡面和空气面的裂纹萌生门槛值也有所差异[53],从图 2可以看出浮法铝硅酸盐玻璃空气面裂纹萌生门槛值高于锡面[58],一方面是由于玻璃出炉运输的过程中锡面与传送带等接触造成其本身缺陷较多;另一方面锡面玻璃的杨氏模量高于空气面玻璃的杨氏模量导致其裂纹萌生门槛值较低。
除了化学强化使玻璃表面产生的压应力影响裂纹萌生载荷以外,玻璃中SiO2的含量也对裂纹萌生载荷具有重要的影响。Gross等[41]研究了SiO2含量从60%(摩尔分数,下同)到100%铝硅酸钙玻璃的抗裂纹性能。裂纹萌生载荷随SiO2含量变化曲线如图 3所示,从图中可以看出摩尔分数为80%SiO2,10%Al2O3,10%GaO的玻璃具有最大的裂纹萌生载荷。
3.2 铝硅酸盐玻璃的亚临界裂纹扩展
水和温度是影响钠钙硅酸盐玻璃静态疲劳的重要因素,其对铝硅酸盐玻璃的静态疲劳同样具有重要的作用。Koike等[59-60]比较了不同假想温度的钠钙硅酸盐玻璃和铝硅酸盐玻璃在干燥和潮湿的气氛中裂纹扩展速率。在潮湿的气氛中,温度越高,钠钙硅酸盐玻璃较铝硅酸盐玻璃的裂纹扩展速率越低。一方面裂纹的扩展伴随着裂纹尖端硅氧键的断裂,高温下铝硅酸盐玻璃中硅氧键断裂的速率更高,因此裂纹扩展的速率更高。另一方面,钠钙硅酸盐玻璃低温下具有更低的黏度,导致裂纹尖端发生一定的塑性变形;高温下钠钙硅酸盐玻璃具有更好的塑性,裂纹扩展需要克服的塑性变形带来的阻力更大,需要更大的能量释放率。
离子交换能够使钠钙硅酸盐玻璃裂纹尖端钝化从而抑制裂纹的扩展,通过离子交换对铝硅酸盐玻璃表面进行化学强化具有相同的效果。Fischer等[61]研究了化学强化对牙用铝硅酸盐微晶玻璃亚临界裂纹扩展的影响,他们发现无论是用单离子(KNO3)熔盐强化还是用双离子(KNO3/NaNO3)熔盐强化,均可显著抑制亚临界裂纹生长。通过单离子强化,裂纹扩展指数n从25增加到52。通过双离子强化,裂纹扩展指数n增加到107,显著提高牙用微晶玻璃的使用寿命。
Jiang等[3]进一步研究了化学强化铝硅酸盐玻璃中亚临界裂纹扩展行为并对玻璃的寿命进行了预测。玻璃在水中分别浸泡24, 48, 72 h的裂纹扩展行为与玻璃在空气中的裂纹扩展行为如图 4所示,图中CS和CT分别是由于化学强化产生的玻璃表面压应力和中心张应力。从图中可以看出,在水中浸泡后的原片铝硅酸盐玻璃和化学强化铝硅酸盐玻璃相较于空气中的裂纹扩展速率增加,而且随着浸泡时间的延长,裂纹扩展速率增加更加明显。采用Paris公式对图中曲线进行拟合可以得到不同状态玻璃的裂纹扩展指数n。拟合结果表明,原片铝硅酸盐玻璃和化学强化铝硅酸盐玻璃的裂纹扩展指数的变化规律与裂纹扩展速率的变化规律相对应。在水中浸泡过的原片铝硅酸盐玻璃与化学强化铝硅酸盐玻璃的裂纹扩展指数小于其在空气中的裂纹扩展指数,而且随着浸泡时间的延长,裂纹扩展指数减小。
上述水浸泡过后的铝硅酸盐玻璃裂纹扩展速率增加是由于铝硅酸盐玻璃的网络结构为[SiO4]-4面体和[AlO4]-4四面体等以Si—O—Si或Si—O—Al键连接。在原子尺度上看,桥接Si—O键的打开对玻璃的断裂过程是至关重要的,而在受力的裂纹尖端会产生高度集中的应变场,桥接Si—O键的应变可以根据减少的键的叠加来讨论,这样就增加了Si和O原子与其他原子成键的可能性。而关于水分子的结构和成键方式O原子轨道2s,2px和2py形成3个杂化轨道,其中的两个与氢原子形成σ键。剩下的孤对轨道远离氢原子。这种排列会产生与孤对轨道相反的正电荷中心。水对裂纹尖端的应力腐蚀作用分为3个阶段,如图 5所示[45]。
第一阶段:在裂纹尖端,环境中的水分子附着在Si—O—Si桥接键。水分子通过下列方式排列:一是与桥氧O(b)形成氢键,二是来自于水中氧原子O(w)的孤对轨道与Si原子相互作用。孤对轨道相互作用包括范德瓦尔斯吸引或者一些Si的未占据轨道的共价键。第二阶段:发生向桥氧的质子转移反应,同时发生从水中的氧原子向Si原子的电子转移。最终形成两个键,一个是Si—O(w)键,另一个是H—O(b)键。而最初的Si—O(b)桥接键被破坏。
第三阶段:O(w)与转移的H原子之间的氢键断裂,并在每一个断裂面上形成Si—O—H。由于氢键相互作用很弱,所以质子转移后这个阶段会迅速出现。当水存在的时候,应变区的表面键会作为一个水分子吸附位点,形成两个Si—O—H表面基团。
图 6是表面压应力、中心张应力与裂纹扩展指数的关系图,从图中可以看出无论是在空气中还是在蒸馏水中,表面压应力越大,中心张应力越小,玻璃的裂纹扩展指数越大,相同条件下产生表面裂纹所需要的能量越高,抑制裂纹扩展的能力越强。裂纹扩展率度取决于表面压应力和中心张应力的综合作用。
根据图 4曲线拟合得到浸泡过后化学强化铝硅酸盐玻璃的裂纹扩展指数并结合式(6),(7)可以对其寿命进行预测(图 7):
|
(6) |
式中:KIi为应力强度因子;σa为服役应力。
|
(7) |
式中σp为保证应力。玻璃的最短断裂时间(服役寿命)与服役应力的平方成反比,并且正比于σp/σa的函数。
与Wiederhorn的钠钙硅酸盐玻璃在水蒸气中的裂纹扩展曲线相比,图 4中铝硅酸盐玻璃的裂纹扩展曲线并没有出现区域Ⅰ裂纹扩展速率随应力强度因子线性增加的阶段,而且区域Ⅱ的平台区域也较短,失稳扩展阶段的曲线是铝硅酸盐玻璃裂纹扩展曲线的主要组成部分。
为了更直观地观察化学强化玻璃裂纹扩展行为以及探究其形貌特征,Tang等[62]采用高速摄像机通过对裂纹扩展过程逐帧观察,分析了裂纹扩展速率、裂纹分叉距离和角度。在冲击能最小的情况下,断口形貌受离子交换过程中形成的玻璃中心张力控制。平均裂纹扩展速率与理论值基本一致,且随着中心张力的增大,裂纹扩展速率呈轻微下降趋势。但裂纹分叉之间距离和角度与理论值不一致。图 8(a)~(c)展示了玻璃分别进行280,300,320 min离子交换后裂纹尖端扩展的图像,表 2对应了图中涉及的相关参数。从图中分叉数量以及距离中可以看出随着中心张力的增大,裂纹分叉之间距离减小,分叉所占比例增大,导致断裂形态更加致密,分叉数随着中心张力的增加而增加。
表 2 图 8玻璃裂纹尖端中心张力、平均裂纹速率、各离子交换能级的分支距离和分支角[62]
Table 2
Central tension, average crack speed, branching distance and branching angles of fig. 8[62]
Ion-exchange time/min |
Central tension/MPa |
Average crack speed/(m·s-1) |
Bifurcation count* |
Trifurcation count* |
Bifurcation distance/mm |
Trifurcation distance/mm |
Bifurcation angle/(°) |
Trifurcation angle/(°) |
280 |
69 |
1825±99 |
9 |
4 |
18±10 |
17±5 |
63±5 |
97±8 |
300 |
72 |
1781±72 |
16 |
18 |
14±6 |
17±4 |
71±5 |
100±10 |
320 |
74 |
1730±60 |
20 |
30 |
9±5 |
10±7 |
66±15 |
104±16 |
Note: *due to the limited resolution and video processing error, some ambiguous branching points are excluded. Also, any branching points within 5 mm of the sample edge are excluded. |
3.3 铝硅酸盐玻璃的动态疲劳
目前铝硅酸盐玻璃的动态疲劳研究才刚刚起步,对相关机理的认识还不成熟。铝硅酸盐玻璃化学强化后表面引入的残余应力同样会影响其动态疲劳行为。Aaldenberg等[63]通过对化学强化铝硅酸盐玻璃的强度和动态疲劳行为进行研究,发现化学强化玻璃表面离子交换层能够抑制裂纹的萌生与缓慢扩展,因而能够较好地抑制玻璃的动态疲劳。但是玻璃的裂纹扩展指数n与离子交换时间和离子类型不具有相关性。未强化铝硅酸盐玻璃的强度具有较大的加载速率依赖性,这与钠钙硅酸盐玻璃相同,动态疲劳与静态疲劳得到的裂纹扩展指数结果一致。然而对于化学强化锂铝硅酸盐玻璃,其强度不具有加载速率依赖性,这就导致计算出的裂纹扩展指数异常大(几个量级的增长),与前期根据化学强化钠铝硅酸盐玻璃的静态疲劳数据得到的裂纹扩展指数相矛盾。因此需要对其动态疲劳裂纹扩展行为进行进一步研究。
4 结束语
本文对硅酸盐玻璃疲劳行为的原理、实验方法及钠钙硅酸盐玻璃与铝硅酸盐玻璃疲劳行为研究进展进行了综述。通过对比钠钙硅酸盐玻璃与铝硅酸盐玻璃的疲劳行为,发现钠钙硅酸盐玻璃原片的裂纹萌生门槛值远低于铝硅酸盐原片玻璃的裂纹萌生门槛值,且化学强化钠钙硅酸盐玻璃与铝硅酸盐玻璃的裂纹萌生门槛值均随表面压应力的增大而增大,但是当表面压应力高于一定应力值时,化学强化钠钙硅酸盐玻璃的裂纹萌生门槛值高于原片玻璃,而化学强化铝硅酸盐玻璃的裂纹萌生门槛值低于原片玻璃。钠钙硅酸盐玻璃与铝硅酸盐玻璃的裂纹扩展速率均随假想温度升高而增加,与钠钙硅酸盐玻璃相比,铝硅酸盐玻璃的裂纹扩展速率随假想温度的变化更大。在动态疲劳研究方面,钠钙硅酸盐原片玻璃与铝硅酸盐原片玻璃的断裂应力均具有加载速率依赖性,而化学强化铝硅酸盐玻璃的动态疲劳断裂应力不具有加载速率依赖性。
尽管前期对钠钙/铝硅酸盐玻璃的疲劳行为有了一定的认识,但是尚有许多问题需要进一步研究,具体包括以下几个方面:需系统研究应力状态和环境因素对化学强化钠钙/铝硅酸盐玻璃静态疲劳与动态疲劳行为的影响,同时前期研究表明,由于化学强化铝硅酸盐玻璃的断裂应力不具有加载速率依赖性,导致得到的裂纹扩展指数与通过静态疲劳数据得到的裂纹扩展指数相矛盾,该问题尚缺乏理论解释和实验数据支持。另外近几年在硅酸盐玻璃领域,发明了通过调控应力分布来控制玻璃强度及缺陷敏感性的方法[64-66],从而提高其使用可靠性,然而化学强化钠钙/铝硅酸盐玻璃的应力分布对其动态疲劳行为的影响有待进一步研究。最后,在采用维氏压痕技术研究脆性材料的动态疲劳行为时,由于维氏压头锥角较大,其产生裂纹的门槛值较高,当压入载荷低于门槛值时,无法产生裂纹,一旦载荷高于此门槛值,裂纹会迅速扩展。此外,较高的门槛值导致压入载荷提高,造成压入深度增大,对化学强化玻璃表面的可控缺陷制备带来了困难(化学强化玻璃的压应力层深度一般仅有几十微米,因此需要更精细的可控缺陷制备技术)。随着近年来纳米压痕技术的快速发展,可以在化学强化玻璃表面进行纳米尺度可控缺陷的制备,从而研究其动态疲劳行为,然而描述含有纳米压痕可控缺陷的脆性材料动态疲劳模型有待建立。