本文所研究的车型是220t矿卡自卸车,无论是空载、满载还是汽车所运行的路面环境都会造成严重的轮胎损耗.而220t矿卡自卸车采用的轮胎型号为40.00R57 XDRB E4R,接近4m的轮胎直径、超乎常规的轮胎重量以及超过10万元的单轮造价使得轮胎磨损成为220t矿卡自卸车最常见的故障.而近乎理想的内外轮转角关系可以将轮胎的非正常磨损降到最低.本文从转向运动学的角度,考虑轮胎侧偏特性的转向关系,以空间坐标下的转向梯形为基础,提出双审判自适应差分进化算法对转向梯形臂、梯形底角等参数进行优化,实现实际内外轮转角关系与阿克曼理论关系的逼近,为解决重型矿卡自卸车轮胎磨损异常、轮胎侧滑等问题提供以转向机构优化为手段的实际工程依据. 1 矿卡转向梯形机构的特性分析 1.1 220t矿卡转向梯形机构模型
220t矿卡自卸车前轴为非独立悬架,通常选择整体式转向梯形,而后置梯形可以较好地避免与车轮的运动干涉,如图 1所示.
![]() |
图 1 220t矿卡自卸车转向梯形机构Fig. 1 Steering system of 220t mining dump truck |
理想内外轮转角关系又叫阿克曼转向几何关系[1].车辆行驶时,只有满足阿克曼转向几何关系,车轮才能纯滚动.实际中,车轮会产生与侧向力相关的轮胎侧偏角.文献[2]中提出,当转向半径较大时各车轮侧偏角大小近似相等,取α11=α12=α2=2°~3°.考虑轮胎侧偏特性的理想内外轮转角关系,如图 2所示.
![]() |
图 2 考虑轮胎侧偏特性的理想内外轮转角关系示意图Fig. 2 Relationship between inner and outer wheel’s corner considering the wheel cornering characteristics |
理想内外轮转角应符合如下关系:
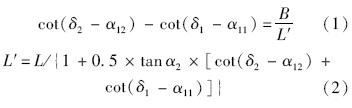
传统的转向梯形研究多数将其直接投影到平面上建立平面模型,然而现实中的转向梯形是以空间形式存在的,出于仿真精度的考虑主销内倾角、后倾角不可忽略,对转向梯形空间运动学理论的研究显得尤为重要[1, 2, 3, 4, 5, 6].
图 3为本文建立的空间转向梯形模型.其中O1,C和E分别代表左侧转向主销中心、转向梯形臂转动节点和球头销中心.设|EF|=L1,|CE|=|DF|=K,Φ和|O1O2|=B分别为转向横拉杆、梯形臂、梯形底角和主销中心距,且|O1C|=|O2D|=L2.
![]() |
图 3 空间转向梯形模型Fig. 3 Steering trapezoid models in spatial coordinates |
图 4分别为左右主销的空间模型.其中β为主销后倾角,α为主销内倾角,在220t矿卡自卸车转向系统中,样车的主销内倾角、后倾角分别为1°和2°.原坐标系绕O1yi1逆时针旋转β得到O1xj1yi1zk1,进而绕Oxj1顺时针旋转α得到O1xj1yj1zj1,通过矩阵T1变换公式如下:

同理有
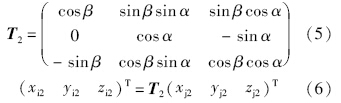
![]() |
图 4 左右主销空间模型Fig. 4 Space model around kingpin |
转向节与梯形臂是固连在一起,故两者转角相等.设δ′1,δ′2为以主销为旋转中心轴的内外轮转角.结合图 3与图 4,E点在坐标系O1xj1yj1zj1中的轨迹方程为

根据式(4)和式(6)可得到E和F两点在Oxyz中的坐标,且有如下关系:
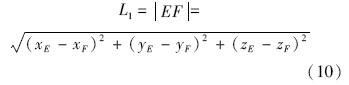
由图 3、图 4中的主销内、后倾角关系可得

由式(1)~式(11)可得到转向内外轮在空间转向梯形模型中绕主销的转角关系:

图 2中的内外轮转角(δ1,δ2)是指绕垂直于地面轴线的转角.在主销空间模型中,如图 4所示,利用矢量转换可得
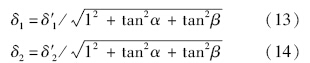
得到实际内外轮转角关系如下:

图 5所示为以主销为旋转中心轴的内轮转角(δ′1)与绕垂直于地面轴线的内轮转角(δ1)的误差.随着δ1的增大,误差呈现线性递增的趋势.
![]() |
图 5 内轮转向角误差(δ′1-δ1)Fig. 5 Inner wheel steering angle error(δ′1-δ1) |
图 6中第1条曲线为ADAMS中建立的220t矿卡自卸车模型实际内外车轮转角关系,第2条是根据转向梯形的空间运动学理论在MATLAB软件中编制程序计算得到的内外轮转角关系曲线,两者基本吻合,证明所建立的空间运动学数学模型是合理的.
![]() |
图 6 ADAMS和MATLAB内外轮转角仿真Fig. 6 Simulation of inner and outer wheel angle in ADAMS and MATLAB |
目前应用到转向机构优化的算法主要包括非线性约束优化算法、遗传算法、粒子群算法等.
本文所设计220t矿卡自卸车样车的内外轮极限转角分别为40°,29.12°;转向梯形臂长为610mm,转向梯形底角为71.85°.在样车数据的基础上,通过ADAMS软件对转向梯形臂长K、梯形底角Φ两个变量进行优化,优化设计界面如图 7所示.
![]() |
图 7 ADAMS优化设计界面Fig. 7 Optimized design interface in ADAMS |
观察原有试验样车内外轮转角关系曲线、理论转向特性曲线和ADAMS优化后的内外轮转角关系曲线三者之间的区别,如图 8所示.
![]() |
图 8 优化前、理论转向与ADAMS优化特性对比Fig. 8 Steering features comparison of original car, theory and ADAMS optimization |
3条曲线在内轮转角小于10°时重合度较高,但是当内轮转角大于10°时重合度较差,因此前轮内外轮转角之间的匹配关系还需要进一步优化,尽可能减小轮胎的磨损.而基于ADAMS软件自带的优化工具箱所得到的内外轮转角优化关系要优于优化前220t矿卡样车转向特性,但是优化的幅度还不够明显,当内轮转角处于15°~30°范围内时,优化后的外轮转角与阿克曼转向几何关系还存在一定的偏差.
分析原因得到:本课题所用优化函数是ADAMS优化工具箱中的fmincon函数,该函数可以解决非线性约束问题,但是要求目标函数、约束函数和梯度都必须连续,而且对初始值依赖性较强,求解容易陷入局部最优值,全局搜索能力较差.有必要引入具有稳定全局搜索能力且可以自适应调整优化参数的优化算法进行转向特性的优化. 3 双审判自适应差分进化算法优化 3.1 双审判自适应差分进化算法概述
目前国内外学者已经将遗传算法应用于转向梯形的优化,而将差分进化算法引入转向系统运动学分析的研究还比较少.差分进化算法是模拟自然界优胜劣汰的一种随机启发式搜索算法,与遗传算法相比有算法编制简单等优点.同时差分进化算法具有动态跟踪当前的搜索情况以调整搜索策略,有较强的全局搜索能力和鲁棒性[7].主要包括变异、交叉、选择3种操作.
变异方法:

交叉方法:

选择方法:

本文采用的双审判自适应差分进化算法的自适应性体现在算法控制参数的自适应[8],实现过程描述为:第1代FLⅠ,CPLⅠ,FLⅡ和CPLⅡ在限制范围内随机生成,将所有成功进化个体的控制参数Fi和CPi组成新的集合FL和CP.随机抽取FL和CP中的元素代替上一代FLⅠ,CⅠPL中成功进化个体的控制参数,未成功进化个体的控制参数继续保留[9].这种参数自适应策略有利于增加种群的多样性,有利于得到全局最优解;同时保证进化过程均采用良好的控制参数,有利于稳定性的提高.双审判向量进化机制[10],有更高的寻优成功率,又提高了收敛的速度,如图 9所示.
![]() |
图 9 双审判自适应差分进化示意图Fig. 9 Dual-trial adaptive differential evolution algorithm |
优化变量为梯形底角Φ、臂长K,如图 3所示. 3.2.2 约束条件
结合设计变量,主要考虑K和Φ的取值范围和转向机构最小传动角约束,有下述约束条件:
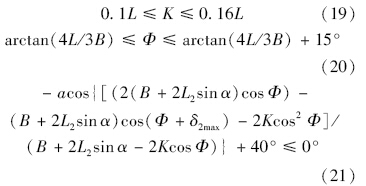
优化目标是求解出最佳转向梯形臂长K和转向梯形底角Φ的组合,使得220t矿卡自卸车内外轮转向角关系曲线与阿克曼转向几何关系曲线重合,实现轮胎的纯滚动减小磨损.考虑到220t矿卡自卸车多数工况的转向角在20°以内,尤其以10°以内的工况使用更加频繁,建立加权函数[10, 11, 12, 13, 14, 15]:

优化目标函数为实际外轮转角与理论外轮转角差值的绝对值:

设置自适应差分进化算法的进化代数为100代,种群数为150,优化结果为K=626mm,Φ=1.1868rad.表 1所示为优化前后结果对比.图 10所示为220t矿卡样车外轮转角、ADAMS优化结果、差分进化算法优化结果等三者与阿克曼理想外轮转角的误差.双审判自适应差分进化算法优化后的效果明显优于220t矿卡样车以及ADAMS优化结果.
结果 | K/mm | Φ/(°) | 最大误差/(°) | 平均误差/(°) |
实际样车 | 610 | 71.85 | 1.36 | 0.74 |
ADAMS优化 | 620 | 70 | 0.77 | 0.41 |
差分优化 | 626 | 68 | 0.82 | 0.19 |
![]() |
图 10 与阿克曼理想外轮转角的误差Fig. 10 Error compared with the outer corner of the ideal Ackerman |
优化前后内外轮转向角关系曲线对比如图 11所示.双审判自适应差分进化算法优化后的内外轮转角关系曲线更逼近理论转向特性,4条曲线在内轮转角小于10°时基本重合,内轮转角超过10°时只有自适应差分优化的曲线与阿克曼转向几何关系曲线重合较好,使轮胎在转向过程中实现纯滚动.
![]() |
图 11 优化前后的内外轮转角关系Fig. 11 Relationship between inner and outer wheel’s corner before and after optimization |
将基于双审判自适应差分进化优化算法得到的K=626mm,Φ=1.1868rad试制成试验样车,针对220t电动轮自卸车做实车轮胎对比性试验[16, 17].试验样车所选轮胎分进口和国产两种型号,试验数据如表 2所示.
试验样车 | K/mm | Φ/(°) | 轮胎寿命/h | |
国产 | 进口 | |||
1 | 610 | 71.85 | 4540 | 10060 |
2 | 626 | 68 | 5070 | |
优化程度/% | 2.62 | 5.36 | 11.67 | 12.20 |
本文区别于常规转向系统运动学研究是针对220t矿卡自卸车这种轮胎异常磨损普遍存在的现象,在建立空间转向梯形坐标的基础上,同时考虑主销后倾角、内倾角造成转向角差异的实际情况,提出以成功进化个体的控制信息选择策略和双审判向量进化相结合的双审判自适应差分进化算法对220t矿卡自卸车的转向梯形进行优化,得到比ADAMS自带的优化模块所优化结果更加逼近理论内外轮转角关系的转向特性曲线.结果表明基于双审判自适应差分进化算法的优化结果可以更好地提高转向性能、减小轮胎磨损,使转向设计更加合理[1].实车轮胎对比性试验表明优化后的转向梯形将220t矿卡自卸车国产和进口轮胎的工作寿命分别提高11.67%,12.20%.
[1] | 刘坚雄. 电动轮矿用自卸车转向系统仿真研究[D].广州:华南理工大学,2013 Liu Jianxiong.Simulation research on steering system of mining dump truck with electric wheels[D].Guangzhou:South China University of Technology,2013(in Chinese) |
[2] | 李玉民,过学迅, 王文家,等.整体式转向梯形的运动分析及优化设计[J].拖拉机与农用运输车,2001(2):18-22 Li Yumin,Guo Xuexun,Wang Wenjia,et al.Motion analyses and optimum design for ackerman steering[J].Tractor & Farm Transporter,2001(2):18-22(in Chinese) |
Cited By in Cnki (24) | |
[3] | 查云飞,钟志华, 闫晓磊.菱形车转向机构的分析与优化[J].中国机械工程,2010,21(8):935-939 Zha Yunfei,Zhong Zhihua,Yan Xiaolei.Analysis and optimization of steering mechanism for rhombic vehicle[J].China Mechanical Engineering,2010,21(8):935-939(in Chinese) |
Cited By in Cnki (3) | Click to display the text | |
[4] | 郭荣,田晋跃, 于英.车辆转向系统的计算机辅助设计[J].汽车工程,2005(5):490-492 Guo Rong,Tian Jinyue,Yu Ying.Computer aided design of vehicle steering system[J].Automotive Engineering,2005(5): 490492(in Chinese) |
Cited By in Cnki (16) | Click to display the text | |
[5] | 崔亚辉,刘晓琳. 重型车辆多轮转向机构的仿真研究[J].中国机械工程,2008,19(20):2501-2504 Cui Yahui,Liu Xiaolin.Kinematical simulation on the steering mechanism for heavy vehicle[J].China Mechanical Engineering,2008,19(20):2501-2504(in Chinese) |
Cited By in Cnki (6) | |
[6] | Gillespie T D. Fundamentals of vehicle dynamics[M].Warrendale,PA:Society of Automotive Engineers Inc,1992 |
[7] | Storn R, Price K.Differential evolution-a simple and efficient heuristic for global optimization over continuous space[J].Journal of Global Optimization,1997,11(4):341-359 |
Click to display the text | |
[8] | Pacejka H B. Tire and vehicle dynamics[M].London:Society of Automotive Engineers Inc,2002 |
[9] | 王前. 基于非线性动力学的FSAE赛车侧向动力学稳定性研究[D].广州:华南理工大学,2013 Wang Qian.Research on the lateral dynamic stability of FSAE racecar based on the nonlinear dynamics[D].Guangzhou:South China University of Technology,2013(in Chinese) |
Cited By in Cnki | |
[10] | Beers K J. Numerical methods for chemical engineering[M].Cambridge:Cambridge University Press,2006 |
[11] | 刘俊,张宏如, 张军杰.大型矿用车转向机构的最优化设计及其运动学仿真分析[J].矿用汽车,2009(2):12-16 Liu Jun,Zhang Hongru,Zhang Junjie.Large mining vehicles steering mechanism to optimize the design and kinematics simulation analysis[J].Mining Truck,2009(2):12-16(in Chinese) |
Cited By in Cnki | |
[12] | 王辉,张文明, 杨珏,等.矿用汽车整体式转向梯形机构的优化设计[J].煤矿机械,2012,33(2):13-15 Wang Hui,Zhang Wenming,Yang Yu.Optimization design of integral type steering linkage for mining truck[J].Coal Mine Machinery,2012,33(2):13-15(in Chinese) |
Cited By in Cnki (3) | |
[13] | 董恩国,张蕾. 基于多目标优化的矿用汽车前轮定位参数-转向机构设计[J].中国制造业信息化,2010,39(3):27-30 Dong Enguo,Zhang Lei.Based on multi-objective optimization of mining truck wheel alignment parameters-steering mechanism design[J].Manufacture Information Engineering of China,2010,39(3):27-30(in Chinese) |
Cited By in Cnki (2) | Click to display the text | |
[14] | Ahmadi J, Ghaffari A,Kazemi R.Fuzzy logic based vehicle stability enhancement through combined differential braking and active front steering[R].ASME Paper DETC2005-85340,2005 |
Click to display the text | |
[15] | Liu Z H, Guy P.Global bifurcation analysis of a nonlinear road vehicle system[J].ASME J Comput Nonlinear Dynam,2007, 2(4): 308-315 |
[16] | Nguyen V, Schultz G,Balachandran B.Lateral load transfer effects on bifurcation behavior of four-wheel vehicle system[J].Journal of Computational and Nonlinear Dynamics,2009, 10(4): 041007-1-12 |
Click to display the text | |
[17] | 杨啟梁. 四轮车辆二自由度转向模型研究[J].机械与电子,2007(8):71-73 Yang Qiliang.Study on the 2-DOF steering model of four-wheel vehicle[J].Machinery & Electronics,2007(8):71-73(in Chinese) |
Cited By in Cnki (2) |